JOB OPENINGS
WORK WITH WIND PROJECTS
Design Manager
Would you like to be a part of the green transition and put your own stamp/imprint on the change needed to achieve the goals of the initiated measures before 2030 then read along here.
Wind Project is a smaller consulting engineering company that works with renewable energy projects.
As we would like to bid on even more energy projects and are experiencing great demand from our customers, we are looking for a skilled colleague to run and manage our planning on current and future projects from start to finish.
We are therefore searching for a design manager within construction with in-depth knowledge of steel and concrete structures. These are tasks that are executed in Denmark.
This is part-time employment, and it can e.g. be a senior who wants to retire from the busy everyday life.
In the role as design manager, you will help lift our projects when they go through the phases of investigation, design and the execution itself. With your competencies and technical proven experience and knowledge, are you already mastering the design manager role. It will be your job to guide and manage the builder safely through design and construction processes and coordinate interfaces between the projecting parties. Furthermore, to prepare organizational and time plans for the design as well as organize decision-making processes and contribute to the preparation of decision-making bases.
You will thoroughly get around the installation subjects and be a sparring partner both internally and externally. It is therefore important that you are skilled at navigating the field of tension between stakeholders and project phases and that you can create strong relations with those you work with. With your insight and knowledge as well as your innovative approach, you can challenge and upgrade the technical solutions.
As a person, you are quality conscious, result oriented structured and creates good results in the collaboration with and through other people. Emphasis is placed on independent handling of tasks and responsibilities where we cherish our informal way of working. Dialogue is an important part of the job and therefore it is important that you are pleasant in your tone of voice, thrives in an outgoing role and have good communication skills.
For further contact:
Poul Martin Wael, owner
mobile: +45 30 37 41 12
e-mail: pmw@projects.as
website: www.projects.as
Ulrik Raahauge, project controller og business developer
mobil: +45 24 24 38 05
e-mail: ulr@projects.as
Projekteringsleder
Vil du gerne være en del af den grønne omstilling og sætte dit eget aftryk på den forandring, der skal til for at nå i mål med de igangsatte tiltag inden 2030, så læs med her.
Wind Projects er en mindre rådgivende konsulentvirksomhed, der arbejder med energiprojekter inden for vedvarende energi.
Da vi gerne vil byde ind på endnu flere energiprojekter og oplever stor efterspørgsel fra vores kunder, leder vi efter en dygtig kollega til at drive og styre vores projektering på nuværende og fremtidige projekter fra start til slut.
Vi søger derfor en projekteringsleder inden for byggeri med dybdegående kendskab til stål- og betonkonstruktioner. Det er projektopgaver, der skal udføres i Danmark.
Der er tale om deltidsansættelse, og det kan f.eks. være en senior med ønske om at trække sig tilbage fra den travle hverdag.
I rollen som projekteringschef kommer du til at være med til at løfte vores projekter, når de skal gennem faserne med undersøgelse, projektering og selve udførelsen. Med dine kompetencer og teknisk dokumenterede erfaring og kendskab, mestrer du allerede rollen som projekteringsleder. Det bliver din opgave at guide og styre bygherren sikkert gennem design- og byggeprocesser og koordinere grænseflader mellem de projekterende parter. Endvidere at udarbejde organisations- og tidsplaner for projekteringen samt tilrettelægge beslutningsprocesser og medvirke til udarbejdelse af beslutningsgrundlag.
Du vil komme grundigt rundt i installationsfagene og være sparringspartner både internt og eksternt. Derfor er det vigtigt at du er dygtig til at navigere i spændingsfeltet mellem interessenter og projektfaser, og at du formår at skabe stærke relationer med dem du arbejder sammen med. Med din indsigt og viden samt innovative tilgang kan du udfordre og opkvalificere de tekniske løsninger.
Som person er du kvalitetsbevidst, resultatorienteret, struktureret og skaber gode resultater i samarbejdet med og gennem andre mennesker. Der lægges vægt på selvstændig varetagelse af opgaver og ansvar, hvor vi værner om vores uformelle arbejdsform. I stillingen vil dialog være en vigtig del af jobbet, og det er derfor vigtigt, at du er behagelig i din omgangstone og trives i en udadvendt rolle og har gode kommunikative evner.
Henvendelse til:
Poul Martin Wael, indehaver
mobil: +45 30 37 41 12
e-mail: pmw@projects.as
website: www.projects.as
Ulrik Raahauge, project controller og business developer
mobil: +45 24 24 38 05
e-mail: ulr@projects.as
Construction Manager/Civil Package Manager
Would you like to be a part of the green transition and put your own stamp/imprint on the change needed to achieve the goals of the initiated measures before 2030 then read along here.
Wind Project is a smaller consulting engineering company that works with renewable energy projects.
As we would like to bid on even more energy projects and are experiencing great demand from our customers, we are looking for a skilled colleague to start up and manage the construction process. In close dialogue with the design manager, you control and supervise that or the construction sites, we work on.
We are therefore searching for a construction manager/civil package manager for design and construction site management of smaller foundation tasks. These are tasks that are executed in Denmark.
This is part-time employment, and it can e.g. be a senior who wants to retire from the busy everyday life.
You have experience from earthwork, transformerstations and industrial construction in smaller scale as well as with construction site management and quality assurance.
Knowledge of the following is an advantage:
- Geotechnics
- Foundation foundry
- Temporary road conditions
- Development of preliminary projects
- Concept description and sketch design
- Quality control in relation to execution of the work
- Discussions with consulting engineers about construction projects and foundations
As a person, you are quality conscious, result oriented and creates good results in the collaboration with and through other people. Emphasis is placed on independent handling of tasks and responsibilities where we cherish our informal way of working. Dialogue is an important part of the job and therefore it is important that you are pleasant in your tone of voice, thrives in an outgoing role and have good communication skills.
For further contact:
Poul Martin Wael, owner
mobile: +45 30 37 41 12
e-mail: pmw@projects.as
website: www.projects.as
Ulrik Raahauge, project controller og business developer
mobil: +45 24 24 38 05
e-mail: ulr@projects.as
Bygningskonstruktør/Entrepriseleder
Vil du gerne være en del af den grønne omstilling og sætte dit eget aftryk på den forandring, der skal til for at nå i mål med de igangsatte tiltag inden 2030, så læs med her.
Wind Projects er en mindre rådgivende konsulentvirksomhed, der arbejder med energiprojekter inden for vedvarende energi.
Da vi gerne vil byde ind på endnu flere energiprojekter og oplever stor efterspørgsel fra vores kunder, leder vi efter en dygtig kollega til at opstarte og lede byggeprocessen og i tæt dialog med projekteringslederen styre og holde tilsyn med den eller de byggepladser, vi arbejder på.
Vi søger derfor en bygningskonstruktør/entrepriseleder til projektering og byggepladsledelse af mindre fundamentopgaver. Det er opgaver, der skal udføres i Danmark.
Der er tale om deltidsansættelse, og det kan f.eks. være en senior med ønske om at trække sig tilbage fra den travle hverdag.
Du har erfaring fra jordarbejde, transformerstationer og industribyggeri i mindre skala samt med byggepladsledelse og kvalitetssikring.
Det er en fordel med kendskab til følgende:
- Geoteknik
- Fundamentstøberi
- Midlertidige vejforhold
- Udvikling af forprojekter
- Konceptbeskrivelse og skitsedesign samt praktisk udførelse
- Kvalitetskontrol ifm. udførelse af arbejdet
- Diskussioner med rådgivende ingeniører ifm. anlægsprojekter og fundamenter
Som person er du kvalitetsbevidst, resultatorienteret og skaber gode resultater i samarbejdet med og gennem andre mennesker. Der lægges vægt på selvstændig varetagelse af opgaver og ansvar, hvor vi værner om vores uformelle arbejdsform. I stillingen vil dialog være en vigtig del af jobbet, og det er derfor vigtigt, at du er behagelig i din omgangstone og trives i en udadvendt rolle og har gode kommunikative evner.
Henvendelse til:
Poul Martin Wael, indehaver
mobil: + 45 30 37 41 12
e-mail: pmw@projects.as
website: www.projects.as
Ulrik Raahauge, project controller og business developer
mobil: +45 24 24 38 05
e-mail: ulr@projects.as
Got an Incredible Project Right Now?
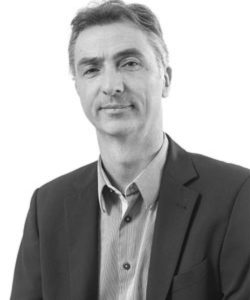
OWNER
POUL MARTIN WAEL
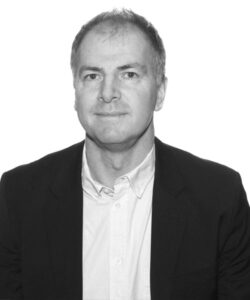